Aluminum extraction is the creation of profiles and shapes by pushing aluminum alloy via a die that has a certain cross-sectional profile. You can use extruded aluminum in some industries as it has excellent properties. Simply, the extraction process is assembling fabrication while improving stiffness and strength.
More so, numerous extruded aluminum alloys are corrosion-resistant, good-looking, lightweight, and have remarkable electrical and thermal conductivity.
Guidelines
Uniformity in Wall Thickness
Ensuring consistency in wall thickness gives a better extrusion efficiency as it lowers the production time, as well as designing a cost-efficient product. You can achieve varying thicknesses.
However, it adds complexity and time to the entire process. Even though raising part cost, by ranging the thickness, one can adjust the extrusion’s mechanical performance in certain locations. It’s vital to note that while cooling, the wall thickness variation results in uneven part cooling, thus potential deformation.
Corners
Did you know that including radii in the sharp corners simplifies the aluminum extrusion? This is so because sharp external and internal corners are challenging to achieve, thus needing additional machining.
Corners that have no radii slow down the production and can result in imperfections. In summary, rounded corners make it easier to extrude the part. Experts advise adding a 0.5 mm to 1mm radius on every sharp corner.
Channel Ratios
For profiles with channels (sometimes known as tongues or pockets), a thumb rule applies whereby the ratio between the channel width and height must approximate 3:1, ensuring you don’t compromise the die strength. Note that the higher the ratio, the more challenging it gets to extrude the part.
Minimum Wall Thickness
Also, it’s essential to make sure the wall thickness isn’t too low. If the wall thickness is insufficient, it could result in problems during the extrusion process, such as incomplete extrusion, higher tool wear, and distortion.
Visual Surfaces
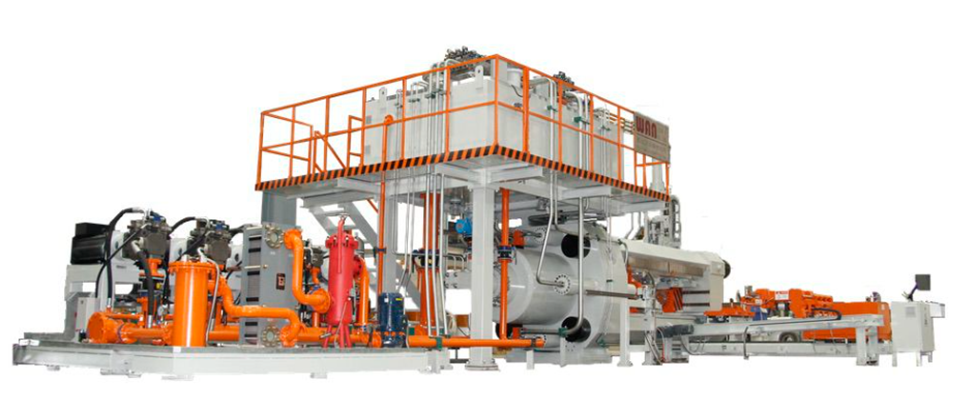
It’s advisable that you create essential visual faces known to your experts so you can create the part with less visual imperfections. Also, consider including a pattern on those surfaces, as it has the benefit of concealing potential imperfections while handling and machining the part.
Geometry
While designing the part, try to utilize easy geometric patterns because the more sophisticated the shape is, the harder it gets to force fabric via the extruder. Also, having a design symmetry is highly recommended, as it lowers peak die stress as the forces are evenly distributed. More so, try to prevent cavities in the design, as this can raise the die lead time, complexity, and cost.
Take Away
Keep in mind that aluminum extrusion is a cost-effective manufacturing process that tends to be long-lasting, highly versatile end products that weigh less but withstand the test of time. For such and a few other characters, extruded parts are in a range of various applications and industries.
There are a few extrusion process limitations, such as dimensional size or tolerances wall thickness. However, it must be given consideration while deciding how great you can achieve the final product since the capabilities and technology are evolving every day.
ALSO READ: The Top 5 Home Automation Companies in India That Redefine Smart Living